overview
Numerous human-made infrastructure (buildings, bridges, dams, highways, tunnels, etc.) in USA and around the world are reaching their life expectancy, and thus have strong needs for routine inspection and maintenance to ensure sustainability. The American Society of Civil Engineers (ASCE) has compiled regular “report cards” on the state of U.S. infrastructure since the 1980s. In its 2017 report, the ASCE found that the nation’s infrastructure averaged a “D+,” meaning that conditions were “mostly below standard,” exhibiting “significant deterioration,” with a “strong risk of failure.” It is estimated that there is a total “infrastructure gap” of more than $2 trillion needed by 2025 [Infrastructure2020]. .
According to Federal Highway Administration (FHWA) report in 2020, of the 617,000 bridges in the United States about 46,000 were in poor condition. This represents about 7.5% of all bridges. FHWA also estimated that eliminating the backlog in 20 years would require an investment of $24.6 billion annually [Bridge2020]. Likewise, as per data from 2017 ASCE report card, the average age of the 90,580 dams in USA is 56 years, and nearly 15,500 (17%) dams are identified as high-hazard potential. It is estimated that it will require an investment of nearly $45 billion to repair aging, yet critical, high-hazard potential dams.
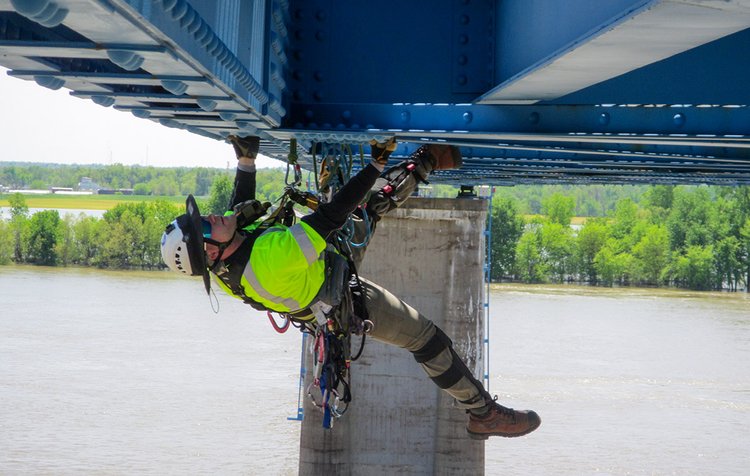
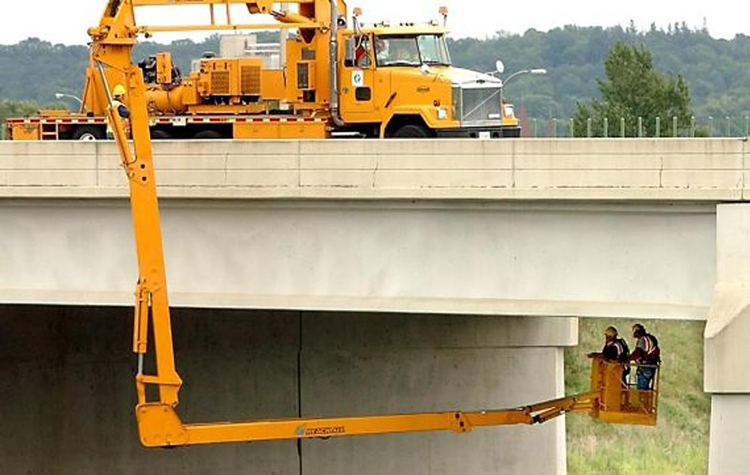
Problem Statements
Our major focus in infrasctructure insepction is to automate the data acquisition process and reduce the harzadous work involved. We didn't do infrasctructure inspection by ourselves. we offer climbling robot based data acquisition service, which help inspection company to collect data in a smart way.
01. Manual Inspection is labor-intensive and dangerous
the current practice of manual inspection of concrete infrastructure using nondestructive testing (NDT) instruments by a “spider-man” with rope access, or by using scaffolding or a boom truck is time-consuming, exposes human workers to potentially dangerous situations, and often requires traffic control that is very expensive to carry out. It is of paramount importance to develop robotic field inspection technologies and data analysis software to automate the inspection process thereby decreasing costs, increasing the inspection speed and improving safety.
02. Subsurface defects need to be detected
In addition to visual inspection of surface flaws (e.g., cracks and spalls), inspectors need to detect subsurface defects (e.g., delamination and voids) and locate embedment items (rebar, pipes, tension cables) using NDT instruments such as ground penetrating radar (GPR) to determine the structural integrity of concrete structures. The GPR is widely used in NDT and geophysics survey to inspect bridge decks, locate and map buried objects (e.g., utilities, rebar, underground storage tanks, metallic or plastic conduits), measure pavement thickness and properties, locate and characterize subsurface defects (voids, delamination).
03. GPR data need to acquired and analyzed in a smart way
Through our more than 200 interviews and 50 site visits with stakeholders, we realized that there are two major challenges to reveal underground objects or subsurface flaws using GPR. The first one is how to determine GPR’s position and orientation accurately and in real time at each GPR sampling step. The second challenge is how to develop an efficient 3D GPR imaging method to visualize the subsurface objects allowing regular non-professional people to understand.
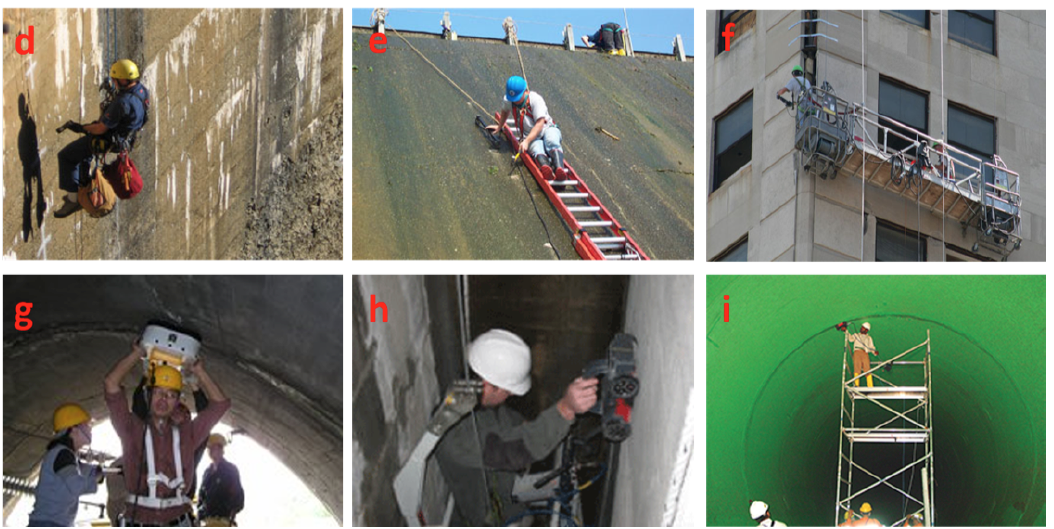
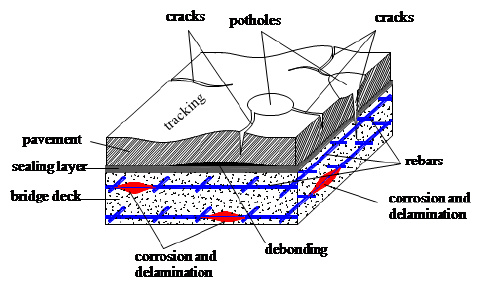
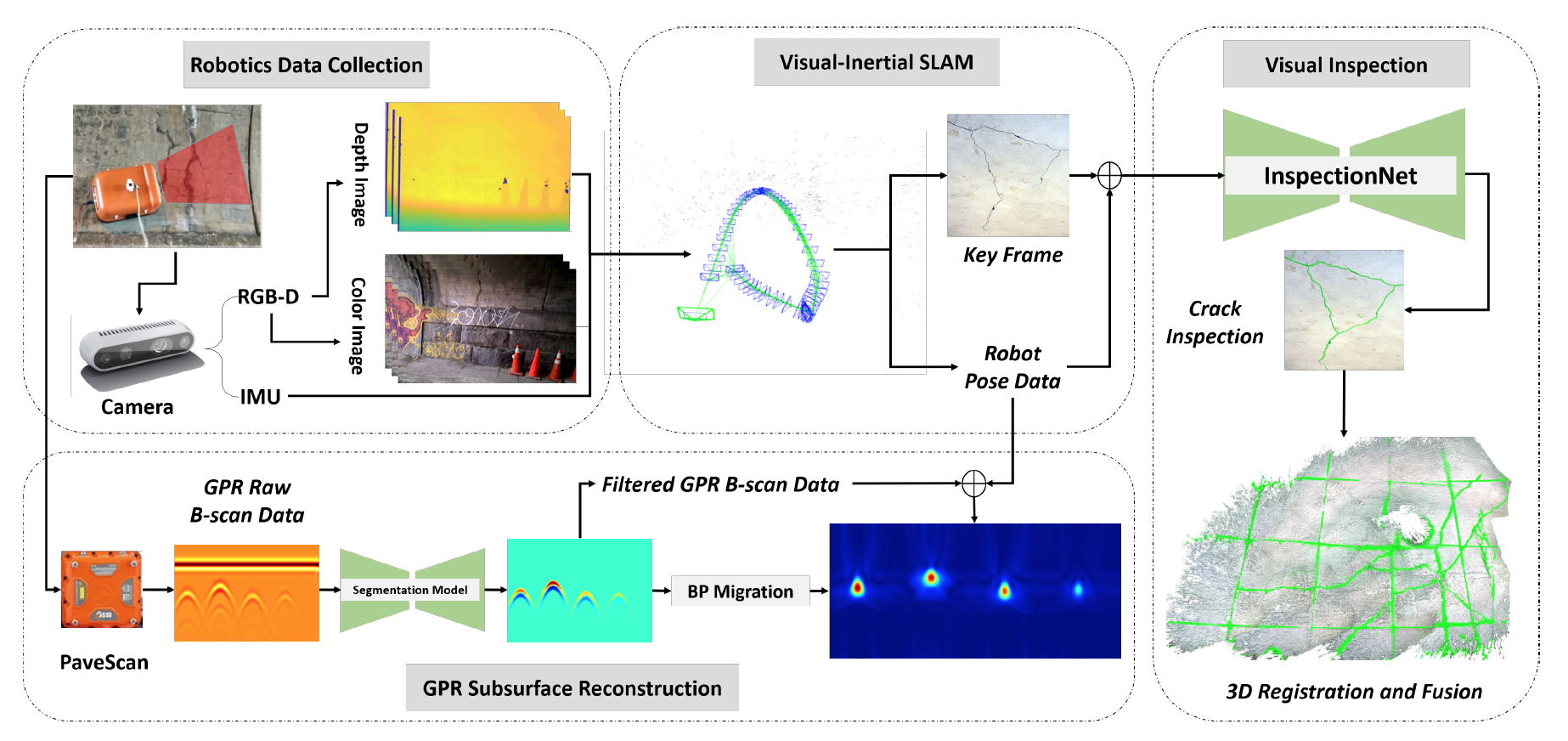
how it works?!
Robotic inspection of infrastructure is an emerging market with minimal participants currently in the field. The driving forces for robotic inspection include: 1) the aged civil infrastructure in USA; 2) shortage of inspectors; and 3) government regulations and investment. Department of Transportation (DOT) has established a University Transportation Center for Inspecting and Preserving Infrastructure through Robotic Exploration (INSPIRE) in 2017. INSPIRE Center is currently embarking on an unprecedented mission to transform the current visual inspection practice of bridges to a future data driven practice based on robotic platforms, including mobile manipulating UAVs, magnet-based robots for steel bridge inspections and CCNY’s wall-climbing robots for concrete bridge inspections. CCNY is one of the six major consortium members of the INSPIRE Center.
Read Morewhy us!
The use of InnovBot’s robotic inspection tool will eliminate the time, hassle and cost to layout gridlines on flat terrain, and make it possible to automatically inspect difficult-to-access locations with minimum human intervention. It will allow the inspection tasks to be performed at least 10 times faster, at a lower cost and increase safety by avoiding costly and dangerous scaffolds. The proposed R&D will advance the state-of-the-art robotic technology and produce climbing machines, vision-based accurate positioning and 3D GPR imaging software as a holistic solution to revolutionize the way the GPR data is collected, interpreted and visualized.
We will also entend our robotic data acquisition to other specialty scenario based on client needs. Customize solution might be needed. Application scenatio include but not limit to following
Submerge parts
Submerge part of bridge, dam etc. Additional sensor might be needed
Underground facilities
Tunnel, Pipeline, Subway or underground system
Underwater or Submarine
Facilities underwater or in submarine enviroment