overview
Wind turbines are manufactured in a wide range of vertical and horizontal axis. The smallest turbines are used for applications such as battery charging for auxiliary power for boats or caravans or to power traffic warning signs. Larger turbines can be used for making contributions to a domestic power supply while selling unused power back to the utility supplier via the electrical grid. Arrays of large turbines, known as wind farms, are becoming an increasingly important source of intermittent renewable energy and are used by many countries as part of a strategy to reduce their reliance on fossil fuels.
One assessment claimed that, as of 2009, wind had the “lowest relative greenhouse gas emissions, the least water consumption demands and… the most favourable social impacts” compared to photovoltaic, hydro, geothermal, coal and gas.[1]
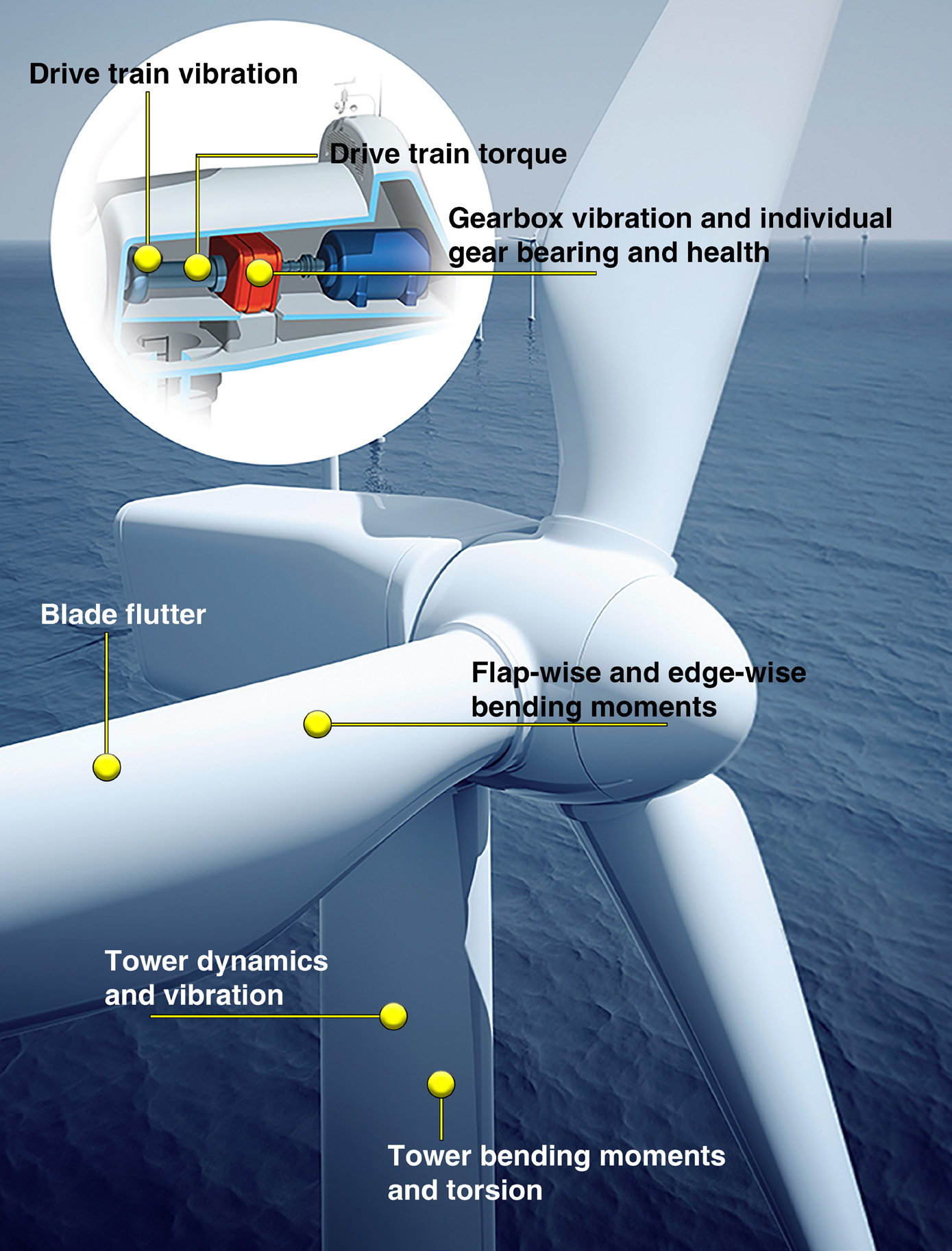
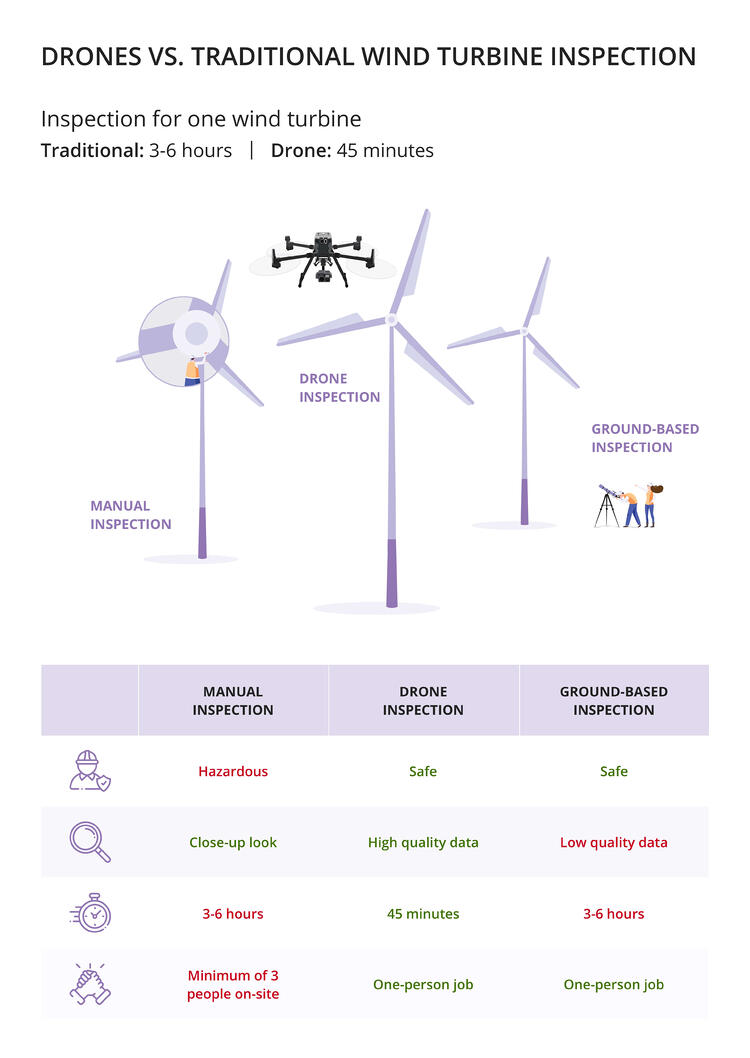
operation and Maitenance cost model
For modern machines the estimated maintenance costs are in the range of 1.5% to 2% of the original investment per annum.O&M costs average between $42,000 and $48,000/MW during the first 10 years of a wind turbine's operations.
- Common commercial wind turbine sizes in megawatts:
- -1.5 MW (onshore, or land-based)
- -2.5 MW (onshore)
- -4 MW (onshore)
- -6-8 MW (offshore)
- -Up to 15 MW (GE Haliade-X produces 12 MW and the Siemens Gamesa SG 14-222DD is a 15MW Turbine)
U.S. wind farm owners are expected to spend over $40 billion on O&M over the next 10 years, and the average age of the North American wind fleet rise from 5.5 years in 2015 to 7 years in 2020, and to 14 years in 2030. Along with that, equipment maintenance and operating costs are increasing significantly, leading operators to focus on performance optimization and cost management. Below is a reference for cost breakdown.
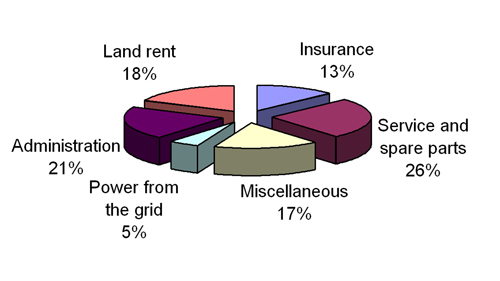
The number of utility-scale wind turbines installed in the U.S. is forecast to rise from 50,000 currently to around 70,000 by 2030. The age of that capacity in 2030 will make the O&M business very lucrative.
Wind Blade Inspection and Maitenance
Among all the cost, the cost of wind turbine blade maintenance is a major one due to wear, tear and harsh environments. The related cost is up to USD $4000 per tower per year. With 400,000+ onshore wind turbines globally, regular maintenance adds up quickly..
One important and often overlooked factor that is affecting the commercial viability of wind energy is the high percentage of blade failures. Globally, it is estimated that there are a total of 3,800 blade failures every year. The cost of damage to wind farms can be huge, with repairs starting at $300,000 for the replacement of just one blade. The remote nature of turbine farms makes it difficult for operators to know when early stage damage is developing. Spot visual blade damage checks and repairs by technicians are both dangerous and costly.
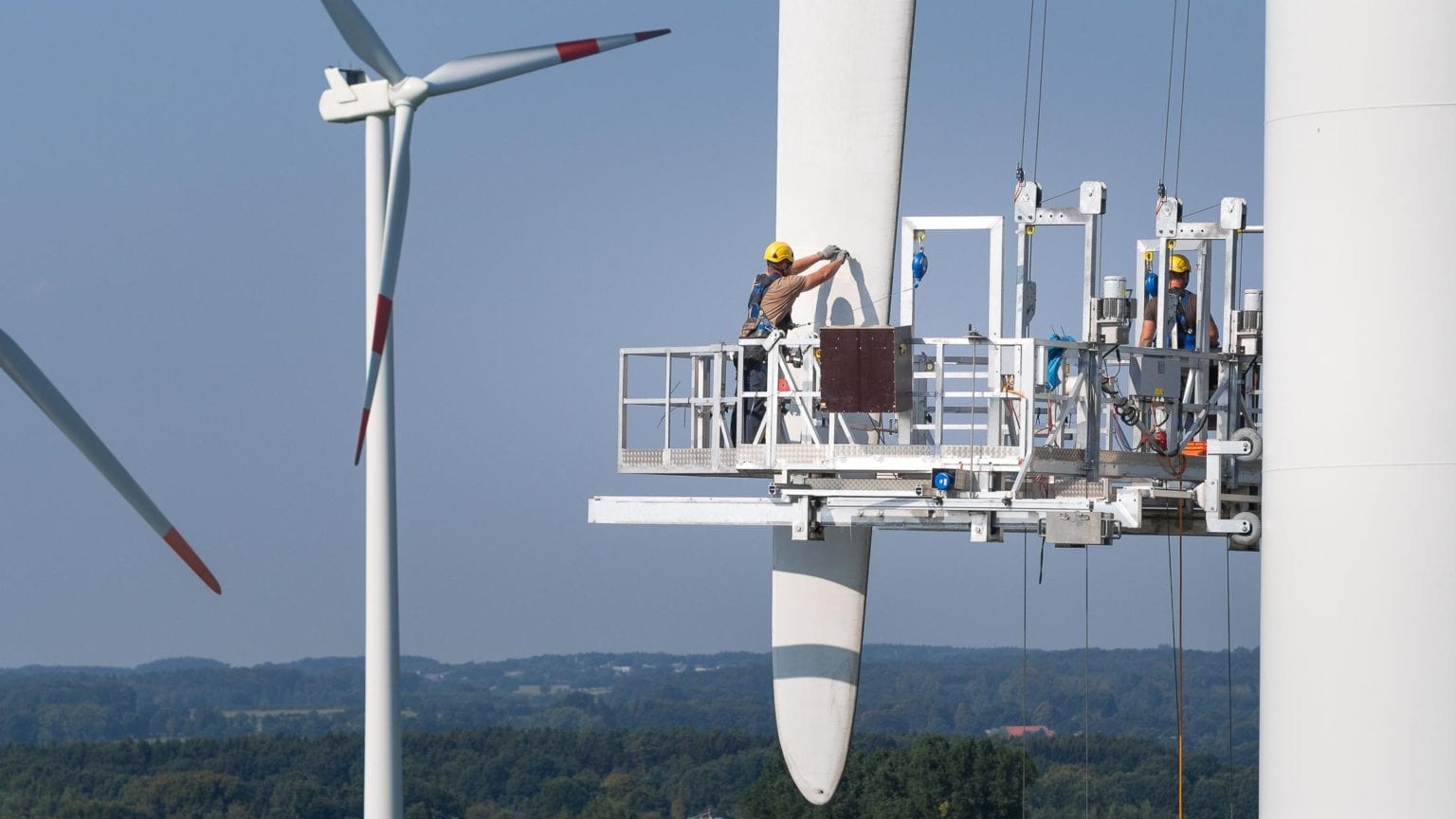
Wind blades are complex structures that are not immune to manufacturing defects. Delamination defects results in a gap between laminates — which ultimately reduces the bearing capacity. The end result in buckling under external loads. The presence of foreign particles in the building resin, gas bubbles and improperly applied structural adhesive are other reasons why a wind turbine is not able to generate optimal performance.Utilizing an efficient inspection methodology (in terms of time and cost) that is able to accurately pinpoint these defects is critical.
There are several traditional ways of inspecting wind turbines. Using rope climbing teams is one of the most common albeit risky ways of inspection. However, Firstly, visually inspecting a windmill is a poor strategy as far as data acquisition is concerned. Secondly, using this inspection method, you can inspect just 2 to 5 turbines every day. Inspection costs could be as high as $1500-$2000 for a single turbine.
Our combination of drone-based visual inspection and climbing robot impact sounding inspection will not only find the problem in first place, but also be able to detect invisible damage or defects in early stage.
01. Drone Inspection
Using automation and drones, you can potentially inspect 20 turbines every day. And a faster inspection process and lesser human intervention means that you can bring down your cost to $300-$500 for a single turbine.
02. Climbing Robot Inspection
with a sophisticated thermal sensor. Using the latest thermal sensors, we can now inspect 15 cm deep into a wind turbine blade. However, if clients need more detailed data, or data besides surface data, especially for questionable blade area. Climbing robot inspection is used.
03. Health check and predictive Maintenance for blade
Inspection is just part of the work. Per client's need, we can integrate data from other monitoring system, establishing blade health management, as well as working closely with cleaning solution providers and blade manufacture for timely repair.
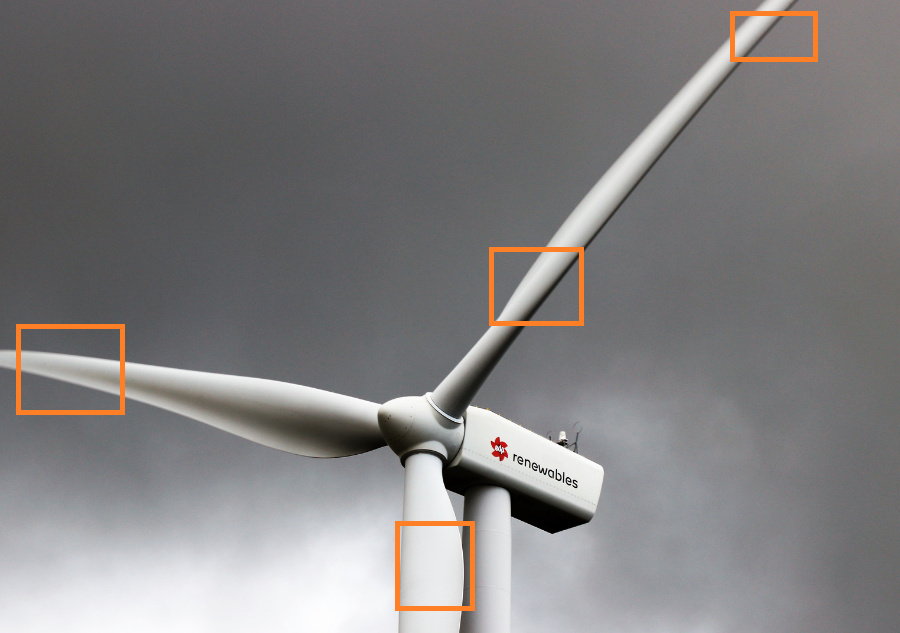
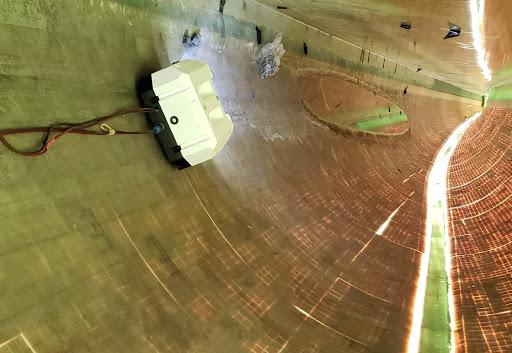
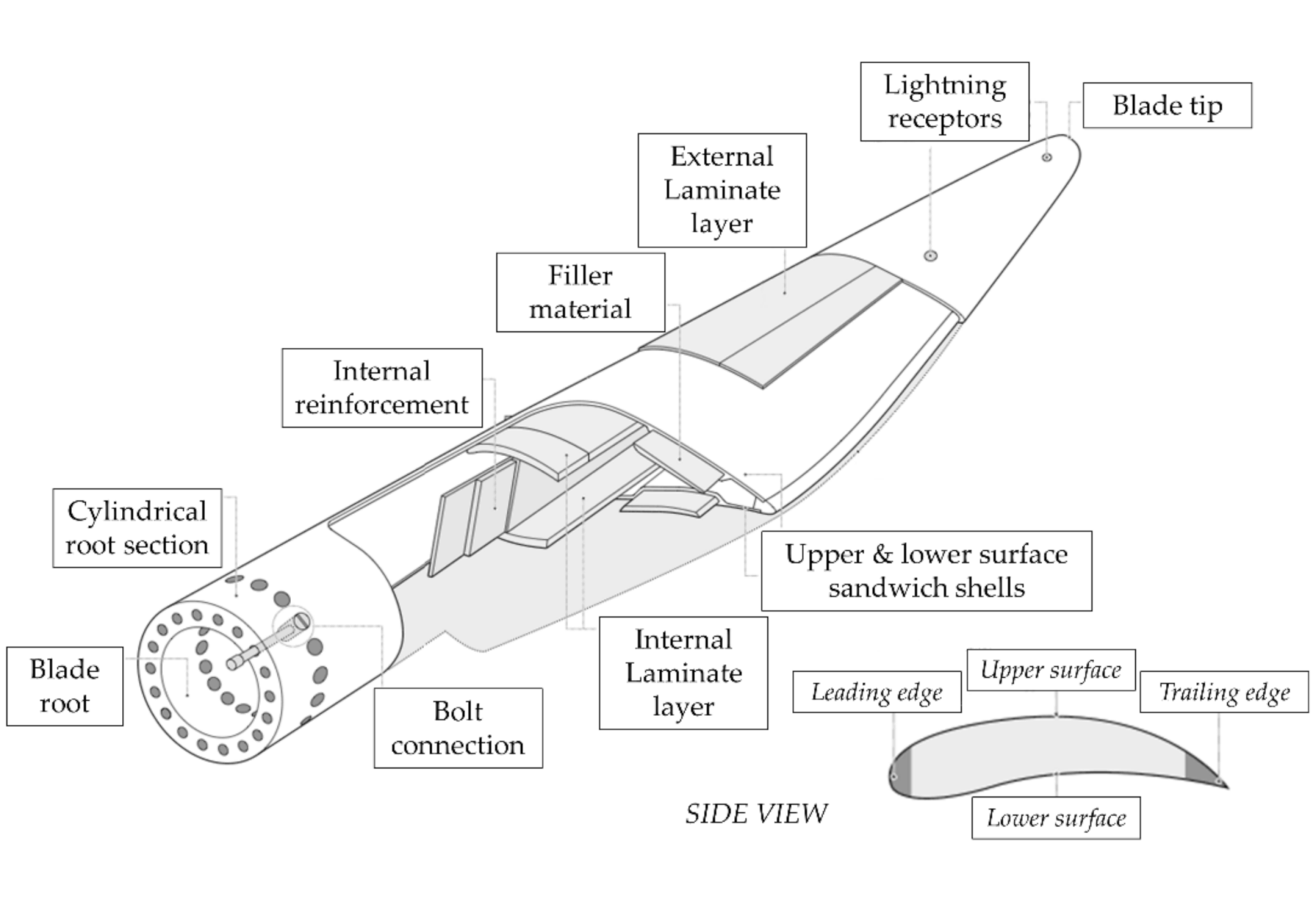
why us!
With our AI-powered drone and climbing robot inspection service, we are able to obtain high-quality data, and find problem quickly. Also we integrate online vibration and acoustic monitoring data, and build up the predictive health management system for blade.